We have a look at each step of the achievement course of during receiving, putaway, order administration, decide and pack, transport and returns.
Rather a lot must occur to get bodily merchandise all the best way from the producer, by way of a warehouse, and into the fingers of a web based buyer.
Order achievement is a necessity for an ecommerce enterprise, however understanding after which mastering every a part of the method could be troublesome. Success isn’t solely about processing every order appropriately and on the lowest doable price, it’s additionally a serious part of buyer satisfaction. Doing an incredible job may end up in glowing suggestions, and doing a poor job can sink your corporation in a short time.
Let’s have a look at the whole lot of the achievement course of, from receiving stock to storage, decide and pack, order administration, transport and what occurs when an order is returned.
What’s the achievement course of?
The achievement course of is the entire journey that your stock takes from being acquired at your warehouse to being shipped out to the client’s door. It includes the arrival of a freight cargo, breaking it down for storage, receiving orders to course of, selecting merchandise from cabinets, packing orders into bins, and transport these bins out.
If the client sends the order again then the method works in reverse, receiving shipments on the warehouse and placing the merchandise again into storage.
You’ll be able to deal with the achievement course of your self, use an built-in service like Amazon’s FBA, or contract it out to a third-party logistics firm (3PL). It’s additionally frequent to make use of a mix of those achievement methods for various merchandise, gross sales channels or geographical areas. You might need your individual warehouse for native orders, for instance, and use a accomplice firm with a number of warehouses for on-line orders.
There are additionally achievement methods like dropshipping, the place the producer or wholesaler sends items on to your buyer, so that you by no means must deal with the bodily product your self. Nevertheless, even then, the achievement course of nonetheless takes place – it’s simply dealt with by another person.
1. Receiving
The receiving course of (or inbound transport) is simply what it appears like. It’s the primary a part of the achievement course of and occurs while you obtain items out of your provider, typically the producer or distributor. Freight shipments are despatched to your warehouse, often through vans. The products are offloaded and your warehouse then must test them and make sure receipt of the correct objects and portions based mostly in your bill.
Stock is then inspected for injury and usually damaged down from massive packaging into particular person models. A warehouse management system (WMS) with barcode scanner assist could be very helpful right here. Scanning every merchandise as it’s processed helps guarantee an correct rely and lets you confirm stock ranges all through.
2. Putaway and storage
After it’s acquired and the cargo checked, your stock is moved to pallets or cabinets in your warehouse. Protecting similar objects collectively and storing them in designated areas for every SKU will velocity up the method of utilizing that stock.
In case your merchandise want processing earlier than they are often shipped out, you would possibly select to do this earlier than they’re put away. This could embody bundling separate objects to create a brand new SKU, or creating totally different multipack sizes of the identical merchandise. A scanner and WMS assist right here as effectively, by making certain that merchandise are mixed appropriately and the brand new stock counts reconcile appropriately with the unique objects.
Create time on your workforce to test items, put them away, and do spot stock counts. It would keep accuracy and assist maintain issues working easily. Prepare your workforce on these processes, particularly how they scan items and confirm them inside your system.
If you happen to use particular gear like a forklift, give each warehouse workforce member coaching on how one can use it and how one can work safely round it. Utilizing the precise gear, retaining items saved in a particular place for every SKU, and coaching groups on how one can transfer round your warehouse will all make your achievement course of considerably extra environment friendly.
When you’ve received the fundamentals, you’ll be able to increase to extra superior layouts and strategies. These embody placing your generally bought stock close to packing stations, creating one-way lanes for individuals to stroll in, and grouping merchandise in order that items generally bought collectively are saved shut to one another.
3. Order administration
The subsequent step within the achievement course of often occurs inside your software program. Order administration connects your ecommerce gross sales channels, similar to marketplaces and purchasing carts, along with your warehouse or 3PL accomplice. The result’s that confirmed orders from all of your gross sales channels are funneled right into a single pipeline.
An order administration system (OMS) removes the necessity to obtain orders from a number of platforms and in several codecs, bettering velocity and accuracy. Your OMS might help outline priorities and queue up the orders accordingly, for instance by placing expedited orders to the entrance of the road. The order listing is then despatched to the warehouse workforce.
Together with a warehouse administration system (or generally mixed with it), an OMS helps keep achievement velocity and accuracy, avoiding mis-picks, incorrect portions and different points that result in buyer complaints and returns.
4. Choose and pack
When an order is able to course of, it’s handed to your workforce of pickers – individuals who actually decide objects off your cabinets. Pickers take a printed order sheet, or use a cell app, then discover each merchandise on the listing. Then they carry all of the objects to finish an order, or a number of orders, to a packing station.
Packers put the merchandise into appropriately-sized bins, together with protecting supplies and any paperwork required. Subsequent, they’ll tape every part up and both print transport labels or add order barcode labels so the proper transport could be added on the subsequent stage. Accomplished packages are dropped at transport stations or on to the loading dockers, or stacked in cages to be moved in bulk at a later time.
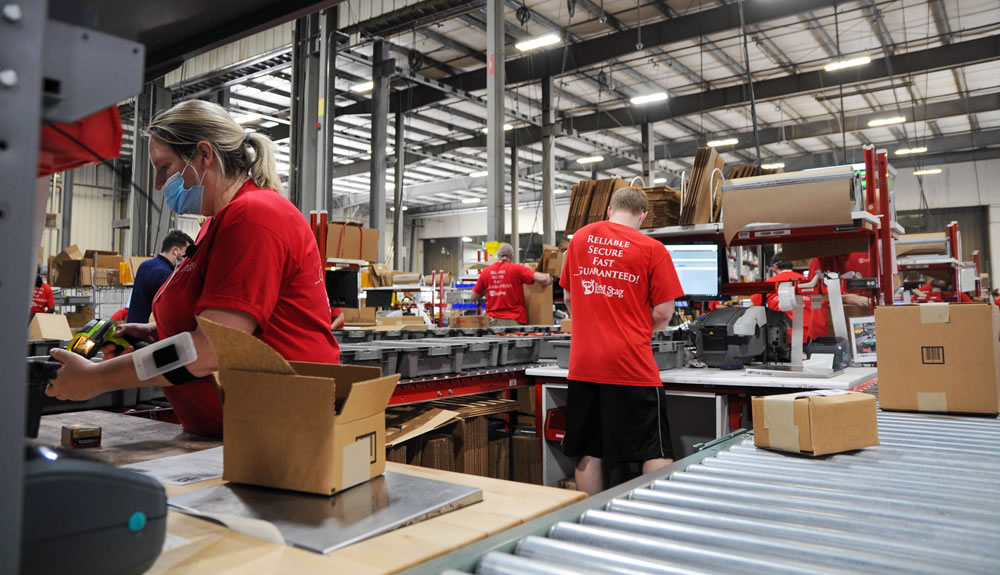
Once more, software program makes the achievement course of rather more manageable. Warehouse administration programs can ship order sheets to particular person pickers to maximise their effectivity. That is particularly helpful to group orders for merchandise in close by areas, and to house out work that requires gear like forklifts or massive carts. It helps workers decrease strolling distances, and keep away from ready to make use of gear that’s in restricted provide.
A WMS that features barcode scanning assist enormously improves accuracy, as a result of every merchandise could be scanned when it’s picked and once more when it’s packed. This serves as a guidelines to make sure that orders are full, and merchandise don’t get switched between orders.
5. Transport
Your warehouse might have separate transport stations, or packing stations might have the flexibility to get orders able to ship. Both approach, the following step is to measure and weigh every package deal, after which purchase a transport label so it may be delivered to the top buyer.
If you happen to use software program to purchase transport out of your chosen carriers, you’ll be able to set it to robotically decide the perfect transport choice to fulfill supply necessities whereas minimizing prices. Checking dimensional weight and precise weight for packages additionally makes it simpler to avoid wasting on transport. Order administration instruments ship all of the required data to your provider’s programs, purchase transport, and print the label for every order.
In case your OMS is built-in along with your gross sales channels, it may well additionally ship monitoring particulars again to {the marketplace} or purchasing cart the place the order originated, or notify the client straight as quickly because the order is shipped. You too can use an OMS to observe the progress of your shipments and arrange alerts for any delays or different points, so customer support workers have all the data they want at hand.
The ultimate step is for all of the packages to be stacked into cages prepared for assortment by the transport provider (or carriers) that you simply use. A printed or digital manifest could also be required, so the provider is aware of which parcels are included. That is often generated by your OMS or transport software program. The provider then comes to gather the packages and, all being effectively, the achievement course of is full.
6. Returns
Sadly, with ecommerce return charges as excessive as 30%, your warehouse must be set as much as deal with returns simply as effectively and precisely as some other a part of the achievement course of. Your customer support workforce must be prepared to speak with clients about returns, refunds, and exchanges so be sure your returns coverage is obvious and straightforward to search out. If you happen to promote on marketplaces like Amazon and eBay, you’ll need to observe the principles they stipulate for returns.
Customer support departments and warehouse groups want coaching on what varieties of returns and exchanges are accepted. This would possibly imply that packaging has not been opened and the unique tags are nonetheless on the merchandise. In fact, you additionally want to concentrate on shopper safety legal guidelines, and their rights to obtain refunds for faulty merchandise or incorrect shipments.
When an order is being returned, you progress into an space known as “reverse logistics”. This covers the method that begins when the client asks to return an order. Often, you’ll must comply with the return and assist the client ship the product again to you. You will want to replace your OMS, which can additionally generate a returns slip and transport label for the client to make use of.
From there, returned items have to be acquired and processed. When the return is acquired, warehouse workers might want to test that the proper product is included and that it’s within the situation you anticipated.
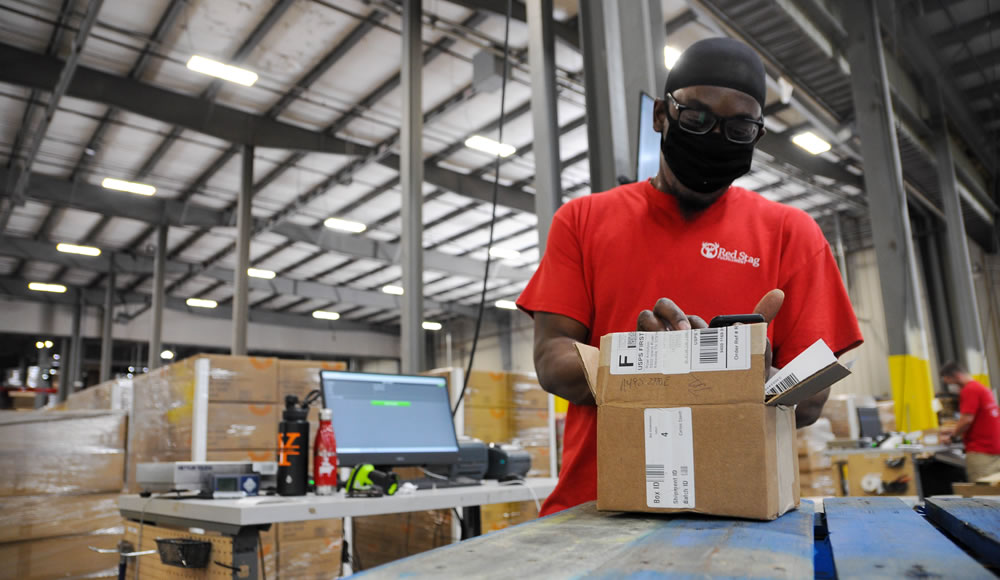
After inspecting the return, so long as every part is as anticipated, a refund could be despatched. Product exchanges observe the identical steps besides that additionally, you will must ship out a brand new order after the return has been processed.
Stock counts could be straightforward to miss within the returns dealing with course of. If somebody returns a product and also you determine that it may be resold, it must be saved on the correct location within the warehouse and the stock rely up to date. This helps forestall reordering merchandise that you simply even have in inventory.
It’s all concerning the individuals
The order achievement course of could be very labor-intensive. You will want individuals to hold out each step and warehouse managers accessible to supply coaching, supervision and assist. Software program makes this simpler as you’ll be able to observe metrics on your general operations in addition to particular person individuals. It could assist determine the place individuals want to enhance and the way your organization can enhance general.
However on the finish of the day, the guts of your warehouse is your workforce. Prepare and assist them on the duties they should carry out. Monitor their successes and supply further studying when it’s wanted. If you happen to determine bottlenecks or areas of concern, sort out them shortly and share this along with your workforce.
Placing your individuals first is a brilliant solution to have a warehouse that runs easily and works collectively.